Combating Contaminants, Shock, and Sunlight in Rugged Display Technologies
May 19th, 2023
Previous innovations in displays have reduced power consumption, allowed lighter and thinner designs, lowered heat production, and allowed for higher resolution pictures. Chassis size was reduced, while clarity and efficiency were increased; however, different industries have different needs and there is not a one-size-fits-all solution. Modern innovations address this by identifying the needs of consumers, commercial, and military use.
The consumer market focuses on size, high resolution, and connectability to other devices and services, while also operating in a well-lit room or office. Contrast this with military use, where deployments can have distinct performance requirements in all sorts of severe operational environments. In-theater use for land, sea and air demands specific high levels of ruggedization which we will be exploring through our rugged displays’ construction materials, along with a process called optical bonding.
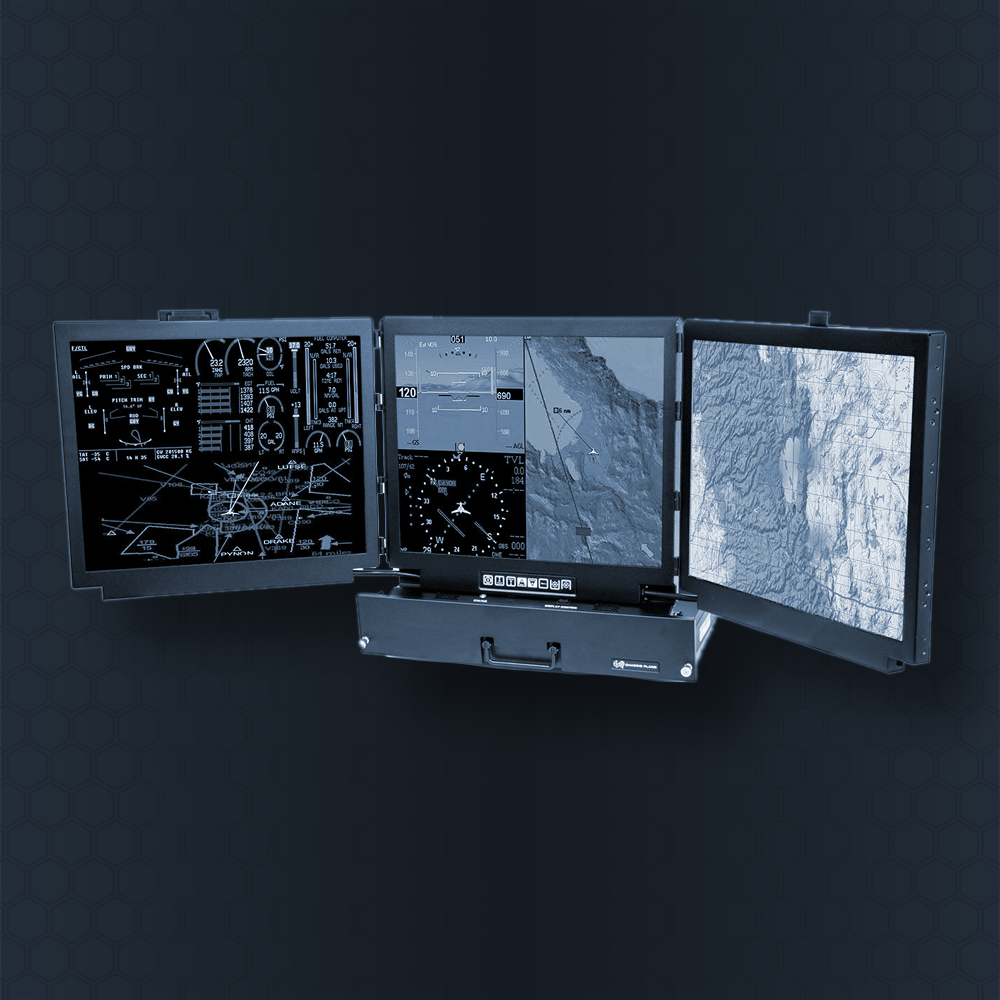
Modern needs for mobility, contaminant protection, and shock resistance
CPNA displays are equipped with a .38” high-strength aircraft grade aluminum front panel, milled to accommodate any customization option. This is the same metal alloy used frequently in aircraft and marine equipment for its amazing thermal conductivity, high fatigue strength, good electrical resistivity, and phenomenal ability to combat wear and corrosion from seawater and salt spray.
In a high static environment such as a dry, low humidity zone, our displays will resist electromagnetic interference (EMI) through the aluminum on the outside, as well as the EMI filters on the optical bonded glass. For sand, salt spray, and other abrasive substances, your equipment faces daily risk of oxidation and general degradation. CPNA displays are built with corrosion-resistant materials that dramatically reduce these effects.
As previously stated, the aluminum used for the front panel has amazing corrosion resistance, but this alone doesn’t protect the interior of the display. For the interior, under the glass, condensation and droplets can form to cause internal damage and corrosion. To compensate for this, we reduce the gap by adding another thin layer of glass, disallowing condensation, and contaminants to enter internally. This process of providing an interior layer for protection and additional visual clarity is called optical bonding.
Benefits of Optical Bonding for Visibility
Optical bonding allows us to deploy displays outside of a well-lit room and still maintain clear readability even in an outdoor environment with fog, or direct sunlight. In conjunction with adding another optical element, the outermost layer of the display has a film known as the vandal shield to prevent impact or scratches.
So far, we have covered corrosion, condensation, EMI, and shock or impact to the frame and top layer of glass. Another issue concerning visual clarity arises in direct sunlight, where a reflection is cast on the display due to a small gap between surfaces. With optical bonding there is no air gap between the cover glass and the actual display. This prohibits the ability for condensation to develop, as well as provide the opportunity to apply anti-reflective coating, and increase the contrast ratio.
Display brightness measured in nits is a key element to sunlight readability, but contrast ratio is the other half of the formula. By increasing contrast, we create much brighter light pixels, and much darker dark pixels, resulting in readability on the extreme ends of lighting conditions.
Optimized for performance for the highest and lowest extremes of our modern, diverse environments, our rugged displays are designed, built, and tested to the stringent standards set forth by our military for temperature, EMI, shock, and corrosion.